

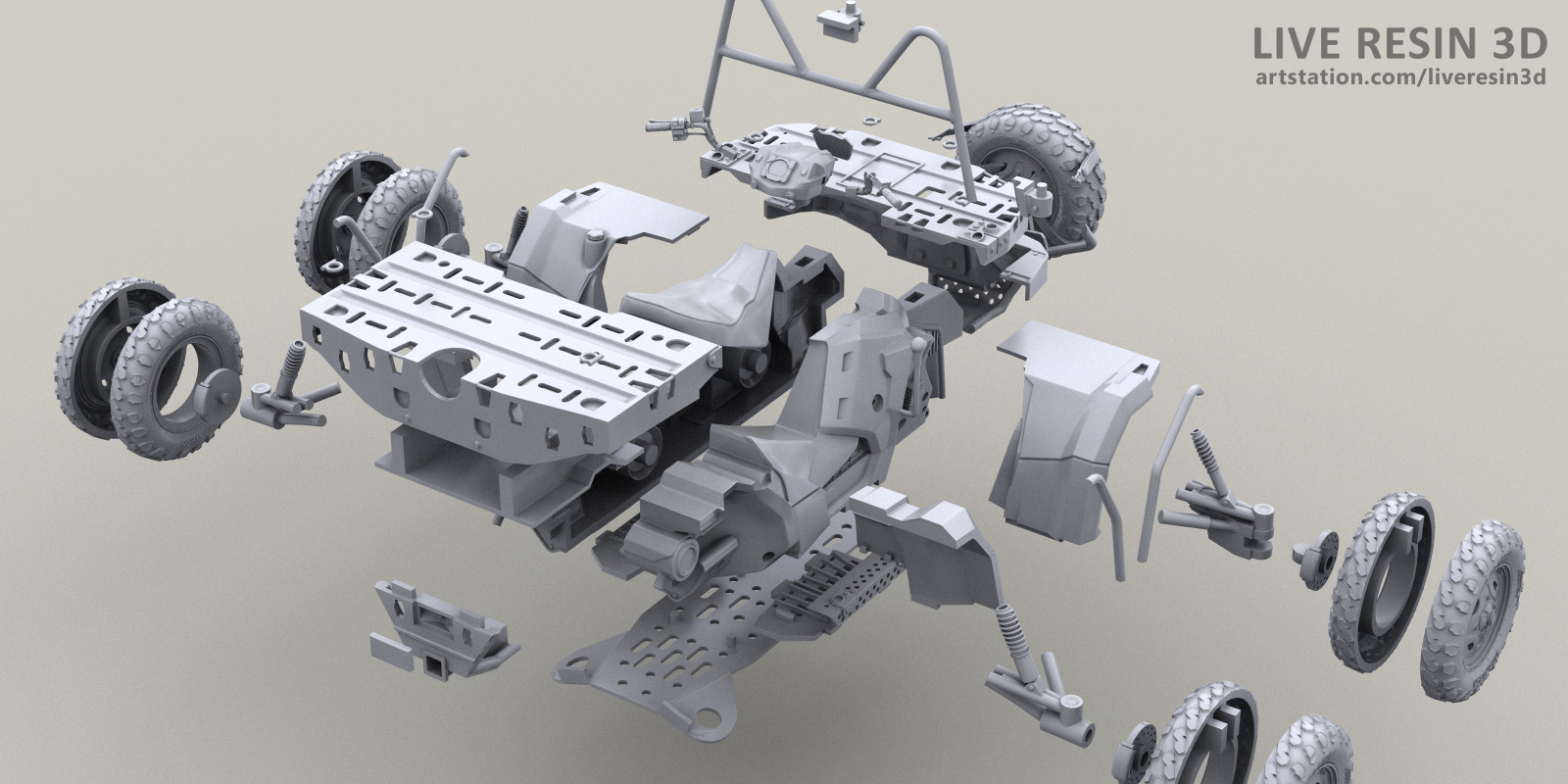
For real-time 3D imaging of prints during tomographic volumetric additive manufacturing, a photo-resin's substantial rise was used in light scattering during gelation. In this study, the authors demonstrated fully simultaneous 3D metrology and printing. Surface profilometry allows for high-resolution photography of local surface topography, but only in relatively flat areas with little deviations from the mean. There is currently no device that can accurately assess the geometry of a complete object during or after printing. These techniques either sample only a selection of layers or presume that the print closely resembles a simple design file. There have been sparse reports recently of AM systems that use optical 3D scanning to assess print geometry between layer depositions. While VAM has increased the speed of AM, the necessity for rapid print metrology and inspection remains a major barrier across all AM modalities. Importantly, VAM processes eliminate the time-consuming peel-recoat phases found in digital light processing (DLP) and stereolithography (SLA), allowing for print times of under a minute. Tomographic VAM is currently the most extensively used VAM method. Recent advances in volumetric additive manufacturing (VAM) have shifted the additive manufacturing (AM) paradigm. Image Credit: MarinaGrigorivna/ Background
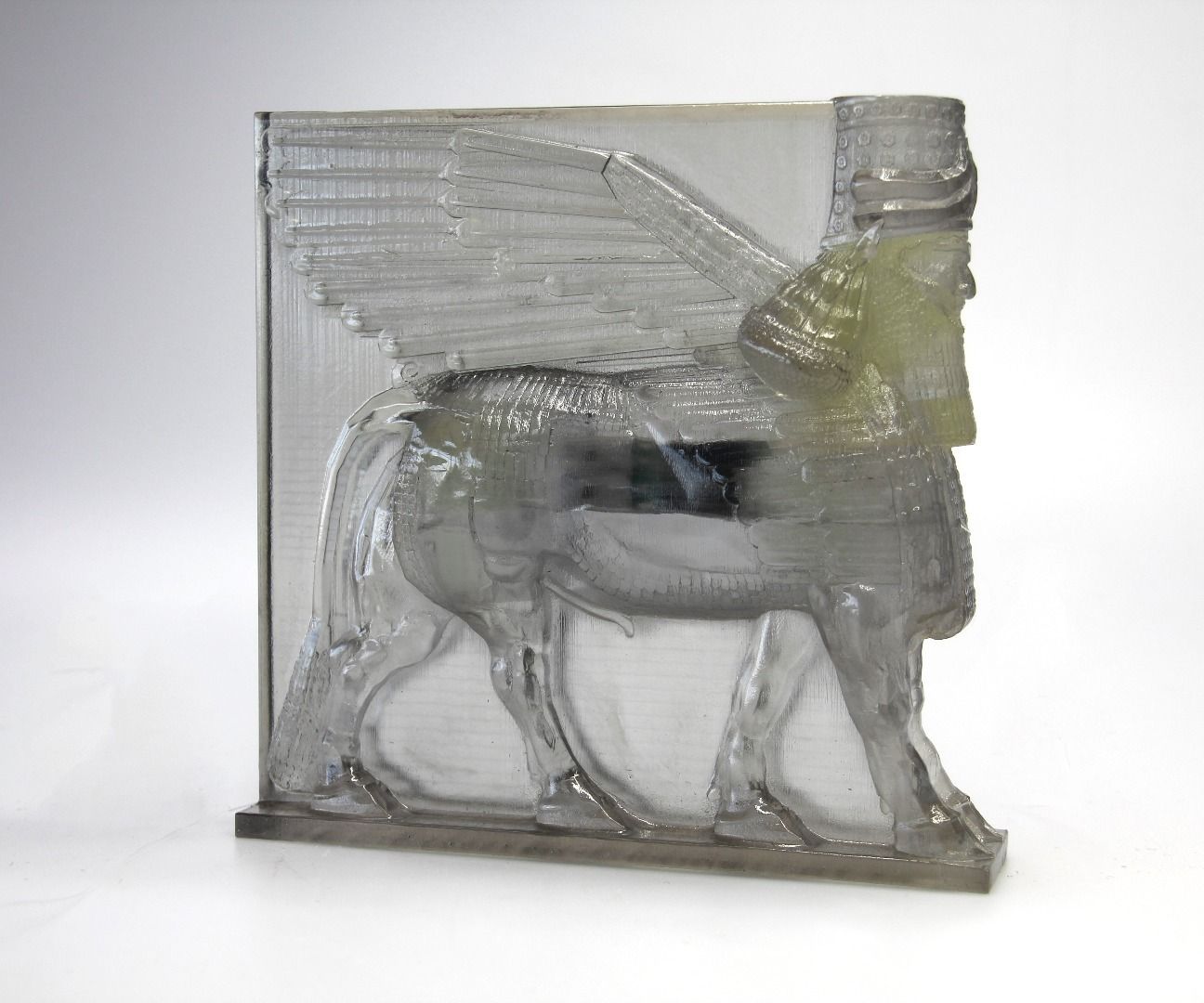
Study: On-the-fly 3D metrology of volumetric additive manufacturing. In an article recently published in the journal Additive Manufacturing, researchers discussed the 3D metrology of on-the-fly volumetric additive manufacturing. By Surbhi Jain Reviewed by Susha Cheriyedath, M.Sc.
